Все двухшнековые экструдеры сталкиваются двумя ограничениями: установленной мощностью двигателя (часто называемой крутящим моментом) и объемной производительностью или приемной способностью.
Производительность или приемная способность любого экструдера зависят от:
- насыпной плотности изменения насыпной плотности во время подачи
- поверхностного трения порошка
- способности материала к текучести
- аэрации
На приемную способность влияет насыпная плотность премикса. Чем выше насыпная плотность, тем выше производительность или кг/час. Например, мелкие частицы порошкового покрытия имеют типичную насыпную плотность 0,2 или ниже, что делает их особенно сложным материалом для подачи.
При подаче материалов в экструдер важно по возможности свести к минимуму аэрацию. Происходит это из-за того, что воздух циркулирует между шнеками и занимает много места внутри экструдера. Создается нестабильный крутящий момент, поскольку воздух находит самый простой путь выхода из экструдера, которым обычно является загрузочное отверстие. Именно этот нестабильный крутящий момент создает напряжение и ведет к потенциальному повреждению валов и редуктора. Это можно сравнить с последствиями вождения автомобиля в режиме постоянного трогания/торможения. Все это приводит к ненужному износу, который, как следствие, влияет на редуктор, валы, шнеки, муфту для передачи крутящего момента и, в некоторой степени, на экструдируемый продукт.
Верхняя подача
Из-за особенностей подачи сверху, когда премикс выпадает из питателя, он подвергается аэрации, что наиболее часто встречается в рецептурах с низкой насыпной плотностью, поскольку их обычно труднее подавать. Одним из способов противодействия аэрации является урезание высоты питателя, что уменьшает возможность попадания воздуха в премикс и способствует повышению производительности. Чтобы устранить эти проблемы в питателях XTS, экструдеры Xtrutech имеют большие прямоугольные загрузочные отверстия и низко расположенные питатели. Мы обнаружили, что в сочетании со шнековыми элементами Xtra-Volume (XV) приемная способность материалов значительно улучшается.
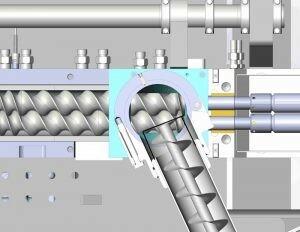
Боковая подача
Тем не менее, самая высокая и эффективная производительность может быть достигнута с помощью опции боковой подачи XTS. Боковой питатель решает проблему аэрации двумя способами: во-первых, питатель находится на одном уровне с боковым отверстием и соединен непосредственно с подающими шнеками XV, что снижает вероятность попадания воздуха вместе с премиксом. Во-вторых, весь захваченный воздух выпускается путем "деаэрации" через верхнее отверстие подачи. Так обеспечивается стабильный крутящий момент, а скорость подачи по сравнению с опцией верхней подачи увеличивается на 30%.
Таким образом, боковая подача идеально подходит для рецептур с низкой насыпной плотностью и более темных цветов, что также позволяет перерабатывать мелкие частицы. По этой причине Xtrutech работает над различными способами переработки мелких частиц, а именно установкой для переработки мелких частиц XTS35.
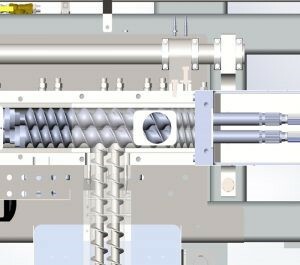
Выводы
Боковая подача максимально увеличит объемную производительность вашего экструдера, поэтому он будет работать с увеличенной пропускной способностью (кг/час). Однако боковая подача может быть более эффективной при работе с определенными рецептурами, например, с низкой насыпной плотностью и с более темными цветами, но не оказывать отрицательного воздействия на общие рецептуры порошковых покрытий.
Для сравнения, подача сверху способствует аэрации и нестабильному крутящему моменту внутри экструдера, что приведет к снижению производительности и сокращению срока службы основных компонентов установки.
Xtrutech предлагает варианты подачи как сверху, так и сбоку, в зависимости от предпочтений наших клиентов. Наша последняя разработка – устройство подачи с безразборной очисткой "на месте" (CIP), которое позволяет нашим клиентам сократить время очистки за счет автоматизации самого процесса.
Вы можете узнать больше о том, какие варианты подачи подходят для вашего экструдера, написав на info@philipp-rus.de